hilion Main menu
All Menu
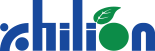
In a roll-to-roll direct coating device, several rolls rotate adjacently and a hopper is used to inject powder between the first and second rolls. The powder is formed into a film and moves along the surface of the roll to the next adjacent roll, becoming thinner and denser. and is finally bonded to the substrate foil between the last two rolls rotating in opposite directions at the same speed.
MORE
A hot ball mill developed by Hilion that can increase the temperature within the rotating vessel to promote homogeneous mixing of the binder and powder and fibrillization of the binder.
Electron micrographs showing the powder of positive electrode active material, conductive carbon, and firillized PTFE from 180℃ for 1hr in this hot ball mill.
The hot roll press ultimately applies heat and pressure to the coated electrode to increase adhesion to the substrate, reduce internal defects, and uniformly reduce thickness
MOREA system that completes electrodes by coating one or both sides and then pressing them in a hot roll press. When dry coating powder or pellets are put into the hoppers, they are calendered as they pass through multiple rolls, adhered to the base foil, and then pressed in a hot roll press to increase the adhesion to the substrate foil and the cohesion of the electrode powder.
MORE
It has the form of agglomerated powder or pellets obtained after mixing raw material powders, and can be manufactured to suit coating conditions.
It is a dry coating powder containing NMC or LFP as the main ingredient and some conductive carbon powder and binder material.
It is made by bonding cathode powder containing PTFE and carbon to aluminum foil. It is calendered after direct roll-to-roll coating, and the thickness is in the range of one-sided coating 40~200 ㎛, double-sided coating 200~500 ㎛ and the coating width is 80 ~ 400㎜. Thickness and width can vary depending on working conditions.
MORE